产品是企业赖以生存的基础,产品数据是企业最基本的也是最重要的数据,产品数据存在于产品设计、采购、生产、销售、服务、库存管理等全过程中。通过对产品设计数据进行编码,并增加采购、库存、生产、制造等属性信息,可以实现对产品相关数据的一体化管理。由此可见物料编码在企业信息化进程中具有重要意义。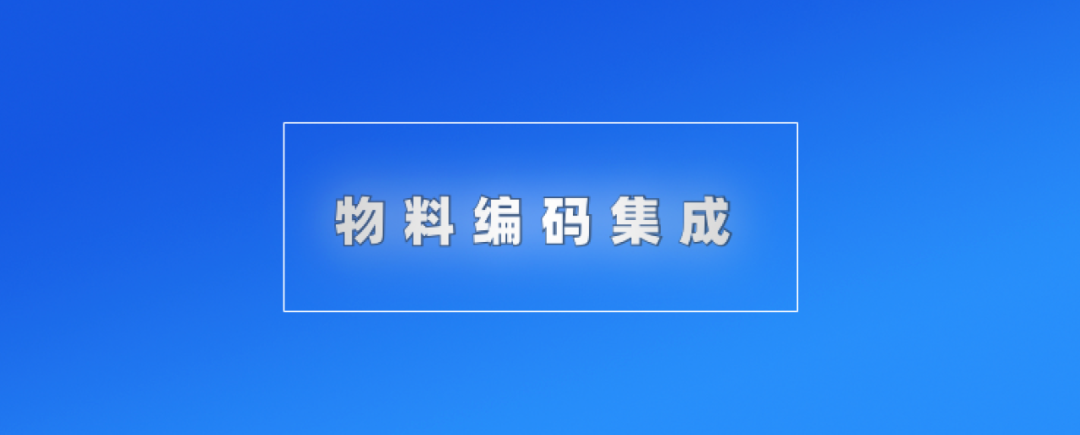
ERP(Enterprise Resource Planning)作为企业资源计划管理系统,具有完整的物料编码管理机制。使用ERP系统的企业,通常在设计图纸审核完成后,手工进行物料编码的创建,并将申请到的编码填写到图纸上。这种模式要求设计者逐张图纸进行物料编码的填写,延长了图纸设计的周期。另一方面,对于外购件和标准件物料,为了避免重复物料的产生,要求物料的创建者或审核者手工进行相似物料的查找,降低了设计的效率。因而,迫切需要一种数据管理系统,能够在图纸设计完成后,自动进行物料编码的创建和填写;在申请标准件和外购件物料时,自动提交物料申请流程,自动进行相似物料的查找,方便设计和审核人员进行重复物料的判断,从而提高图纸设计效率,缩短研发周期,节约设计成本。PDM(Product Data Management)主要管理产品数据、工程数据文档、工程图库、工艺过程文件等。PDM系统本身也有一套编码系统,设计数据检入后会得到相应的编码。对于已经实施ERP的企业,由于存在大量的历史物料,使得PDM系统产生的编码并不能直接使用。这就需要通过PDM与ERP系统之间的信息集成,将PDM系统中的编码转化为ERP中的物料编码,保证产品物料编码的一致性、唯一性,统一物料编码产生的源头。本文主要针对先实施的ERP后实施PDM系统的企业,提供一种物料编码集成的思路。
PDM系统作为设计数据的源头,要从ERP系统获取物料编码,就必须向ERP系统传递物料数据。PDM与ERP物料数据的集成主要取决于ERP系统的需求,表1列出了PDM与ERP物料主数据集成的部分字段。在PDM系统中,物料数据的传递以部件(Part)作为载体,部件的属性参数包括了所有集成字段的数据。根据部件生成方式的不同,其属性参数的获取分为两种情形。一种是直接创建部件,手工填写部件属性参数;一种是通过检入CAD文档,自动生成部件,并获取属性参数。部件创建完成后,PDM系统会产生临时编码。对具有临时编码的部件提交物料编码申请,流程的节点可以根据需求设定,并对每个节点配置相应的角色。部件通过物料申请流程后,通过XML文件将物料信息传递给ERP。ERP接到物料信息后,按定义好的编码规则生成物料编码,再通过接口程序将物料编码回传至PDM系统。这样,部件的临时编码就转变为ERP的正式编码。图1为PDM系统和ERP系统数据传递框图。
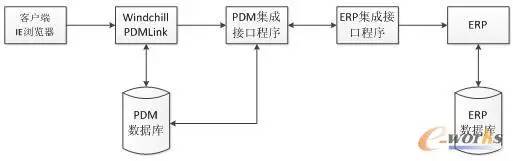
图1 PDM与ERP系统数据传递
在产品设计中,标准件和外购件的使用量较大。由于物料编码规则不完善,物料申请流程控制不严格等因素,使得一个物料出现多个物料编码,给设计、生产诸多环节带来不便,造成数据断裂,影响数据的完整性与准确性。重复物料控制技术的涵盖面较广,一般根据客户使用需求定制开发,本文主要从物料描述合成、物料编码申请流程、相似零部件检索等几个方面进行阐述。物料编码和物料描述是ERP中两个重要参数,每个物料都有自己的物料编码和物料描述。物料描述不相同,ERP系统就会分配不同的物料编码。由此可见,物料描述的规范性,对于控制一物多码问题至关重要。在PDM系统中,可以根据部件的主要参数合成基本物料描述,对于特殊参数和信息通过添加备注的方式实现。当然也可以对标准件和外购件进行分类管理,并根据分类和分类属性值按某种规则自动合成物料描述。物料申请主要是通过流程控制对物料进行审核,流程的节点可以根据需求设定,并对每个节点配置相应的角色。物料申请环节的主要目的是保证进入PDM系统物料数据的唯一和规范,在数据源头控制重复物料的出现。对于ERP中的历史物料,由于存在一物多码问题,在进入PDM系统时,原则上讲都应经过物料申请流程。
对物料进行分类管理的企业,可以通过零部件分类自动触发物料申请流程。在创建部件时指定其分类,当分类属于标准件和外购件时,系统自动触发物料申请任务。一般情况下,审核人员在对申请物料审核时,要根据申请物料的参数值,手工进行模糊搜索,排除重复物料的存在。这使得物料审核时间变长,降低了审核效率。为了提高物料申请审核效率,在物料申请任务中自动检索并列出相似物料,方便申请人员和审核人员物料检查。相似零部件检索的条件较多,一般分为两大类。一种是根据物料主数据的基本参数,如物料型号、物料规格等,进行相似零部件检索;一种是根据零部件分类,在同一分类中检索分类属性值相同的物料。
当新增物料数量较少时,可以采用上述方式逐个申请。但对于新产品设计,由于新增物料较多,再采用上述申请方式,会大大降低设计效率,延长研发设计周期。另一方面,如果在图纸审核前申请物料编码,可能会造成物料编码的浪费。最好的解决办法就是在图纸通过审核后发布之前,由后台完成物料编码的申请,并将申请到的物料编码反填到图纸上。具体流程:设计产品图纸,有物料编码的填写到模型参数CNINDEX中。图纸设计完成后检入PDM系统,系统根据模型参数自动生成部件,当CNINDEX不为空时,PDM系统读取CNINDEX值作为部件编码;当CNINDEX为空时,PDM系统为部件提供临时编码。将整套图纸提交签审流程,图纸批准后,进入物料编码处理程序。程序将遍历结构中的每个部件,按照定义规则形成XML中间文件。如果部件编码为物料编码,PDM将数据传递给ERP后,ERP会对这个物料编码进行同步更新,保证数据的一致。如果部件编码为临时编码,PDM将数据传递给ERP后,ERP会根据物料信息生成新的物料编码。新物料编码回传至PDM系统,替换部件的临时编码,同时赋值给CNINDEX,更新图纸信息。XML中间文件格式如下表所示:

表2 PDM与ERP集成中间文件格式
以PDM系统作为设计数据的源头,从ERP系统获取物料编码,有效解决了因先实施ERP而存在大量历史物料的问题。物料描述合成、物料编码申请、相似零部件检索等编码控制技术,可以避免重复物料的产生,保证产品数据的一致性、唯一性。物料编码返填技术,提高了物料编码获取效率,缩短了图纸研发周期;避免了无效物料编码的产生,节约了企业管理成本。
本文作者宁吉平、张震威、何志敏。